JOSCAR Zero Help & Support for Suppliers
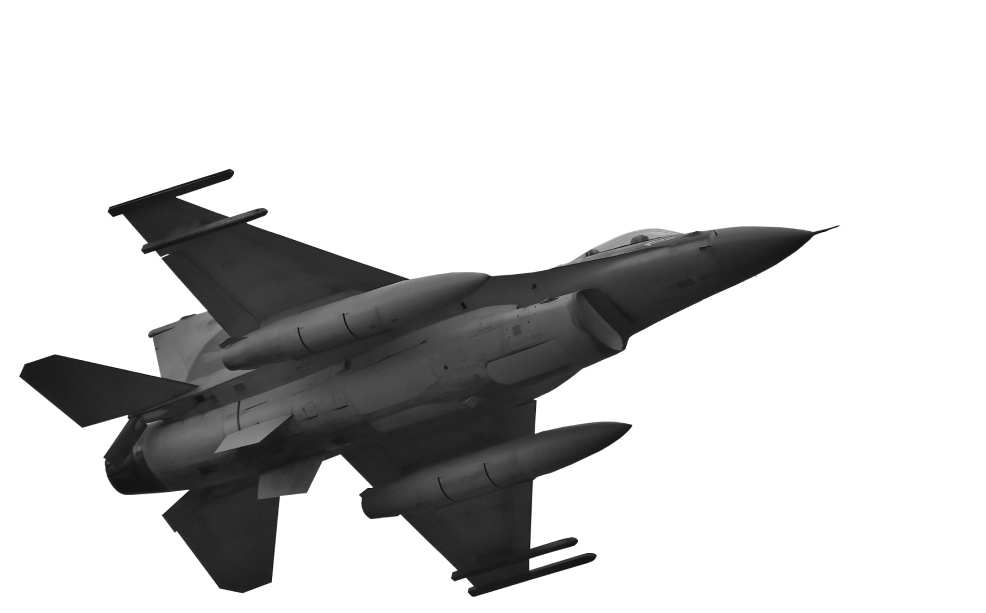
Sections
- Introduction
- Green House Gases and Net Zero
- What are Greenhouse gas emissions?
- How do we calculate greenhouse gas emissions?
- What are Scope 1, 2 and 3 emissions?
- What is Net Zero?
- What are the benefits for business in monitoring greenhouse gas emissions?
- Why is this of benefit to a buyer?
- Why is this of benefit to a supplier?
- Completing your JOSCAR Zero questionnaire
- Scope 1
- Natural Gas
- Liquid Petroleum Gas (LPG)
- Diesel
- Petrol
- Heating oil/kerosene
- Fuel oil
- Gas oil
- Combined heat and power (CHP) system
- Biomass (non CHP)
- Refrigerants
- Scope 2
- Grid electricity
- Supplier specific emissions factors
- Zero emissions contracts
- Renewable energy
- Heat and steam
- Scope 3
- Guidance on estimating data
- How to upload documents
- Buyer specific questions
- How to submit the questionnaire
- How to get help and support
- Understanding your JOSCAR Zero Dashboard
- Understanding your JOSCAR Zero Carbon Action Plan(s)
- What is a Carbon Action Plan?
- What are the benefits of Carbon Action Plans?
- Where can I find my JOSCAR Zero Carbon Action Plan(s)?
- When do I need to update my information?
- How can we use our JOSCAR Zero Carbon Action Plan(s) to our benefit?
- Who will have access to our Carbon Action Plan(s)?
- How have our Carbon Action Plan(s) been tailored to my company?
- Maintaining your JOSCAR Zero questionnaire
Introduction
This document provides guidance for the completion of the JOSCAR Zero questionnaire. It introduces the concept of GHG emissions and how they are calculated, explains the importance of understanding them, and sets out step-by-step guidance for responding to the questionnaire.
What is JOSCAR Zero?
JOSCAR Zero provides buyers with visibility of the carbon emissions within their supply chain, using the collection of supplier site consumption data. Buyers are able to nominate the sites they need information on and Hellios manages the process:
Green House Gases and Net Zero
What are Greenhouse gas emissions?
Greenhouse gases (GHGs) are a group of gases that trap heat when they reach the atmosphere, and cause an increase in the Earth's temperature.
There is a natural level of GHGs in the atmosphere, however as human activity has increased over the past 300 years, the amount of GHGs has increased. This is causing changes such as an increase in the Earth's temperature, changing weather patterns (such as storms, droughts, rainfall), and changing natural features such as glaciers and ice caps.
GHGs reach the atmosphere from human activities such as the burning of fossil fuels e.g., oil and gas, transportation, manufacturing, and farming.
How do we calculate greenhouse gas emissions?
The most widespread GHG is carbon dioxide (CO2), and this is used as a standard measure for GHG emissions by converting all other GHGs to the equivalent mass of CO2. This unit is referred to as a tonne of carbon dioxide equivalent, tCO2e.
The GHG emissions arising from human activities can be calculated by using conversion factors, known as emission factors. These are expressed in terms of kgCO2e per unit of activity. The denominator for the emission factor will depend on the activity type.
This can be carried out for many industrial activities such as burning of natural gas, disposal of waste etc. A company can perform this for all activities at its site that contribute to the emission of GHGs to determine their total emissions. This is often known as a carbon footprint.
What are Scope 1, 2 and 3 emissions?
A carbon footprint consists of three scopes of emissions; Scopes 1, 2, and 3 as defined by the GHG protocol which is the world’s most widely used GHG accounting standard. These scopes include different emissions sources and are a way of looking at the level of influence that a company has over different aspects of its emissions.
Scope 1
Scope 1 covers emissions that occur directly from assets owned and/ or operated by the company such as burning natural gas in boilers, running refrigeration units, and using petrol in company vehicles.
Scope 1 emissions are those over which the company has the most control and is able to make direct changes to impact.
Scope 2
Scope 2 covers emissions from the generation of purchased energy outside the boundaries of the site, that is then consumed by the site.
The purchased energy can be electricity, heat, steam, or cooling purchased from a third party.
Sites can make efforts to reduce emissions in this category through energy efficiency initiatives such as switching to low energy lighting and choosing to purchase from low-carbon energy providers.
Scope 3
Scope 3 emissions often represent the largest part of the carbon footprint.
These emissions are a consequence of a company's activities but occur from sources it does not own or control.
For example, employee business travel and commuting, and supply chain activities.
Scope 3 emissions are broken down into 15 categories but not all 15 categories will apply to all companies. Where they apply to a company, they may not be applicable to all sites. Some of the most common are:
- Business travel - calculated from the distance and modes of transport used by company staff on work related trips.
- Purchased goods and services - calculated from the emissions associated with the production of raw materials or services (e.g., pest control) used by a company as part of their activity.
- Waste generated in operations - calculated from the amount of waste produced by a company at its sites and the chosen methods of treatment.
- Employee commuting - calculated from the distance and modes of transport used by company staff travelling to and from work.
What is Net Zero?
Net zero is considered an important goal in the fight against climate change, as it is seen as a way to limit the increase in global temperature to within 1.5°C above pre-industrial levels, the target set by the Paris Agreement on climate change. Many countries, organisations, and individuals around the world have pledged to reach net zero emissions by a specific date.
In 2019, the UK government set a target to reduce greenhouse gas emissions by 100% from 1990 levels by 2050, this is commonly referred to as net zero. More information can be found here - https://www.gov.uk/government/publications/net-zero-strategy
What are the benefits for business in monitoring greenhouse gas emissions?
Greenhouse gas monitoring is another tool that companies can use to review their resource consumption and identify hotspots or opportunities for cost savings.
Many of the greenhouse gas sources that occur at production sites are related to cost intensive processes such as steam generation and logistics.
Businesses have many stakeholders that they have to work with. In recent years, stakeholders have used their influence with businesses to demand action regarding GHGs, examples are:
- Customers wanting to purchase from companies that use 100% renewable energy
- Investors wanting to invest in companies with net zero targets
- Large scale government contracts being dependent on service providers having net zero targets and action plans
Many companies choose to monitor greenhouse gas performance and publicly report this information as part of their annual financial reporting. In the UK it is a requirement to report greenhouse gas emissions performance as part of an annual report under the Streamlined Energy and Carbon Reporting Regulations (SECR) if a company meets two or more of the following:
- Turnover (or gross income) of £36 million or more.
- Balance sheet assets of £18 million or more.
- 250 employees or more.
Large and small organisations that demonstrate management of their emissions can experience numerous advantages. This can include attracting environmental investors and demonstrating better environmental performance than competitors, potentially leading to business opportunities.
Why is this of benefit to a buyer?
Companies are being asked by stakeholders such as investors, customers, and governments to act on reducing their greenhouse gas emissions and contribute to achieving net zero.
The first step on the path to net zero for many buyers is collecting information on the carbon footprint of their value chain partners, such as suppliers. This will involve collecting information on emissions data from suppliers and the JOSCAR Zero questionnaire will be used to provide this service to buyers.
Along the journey to net zero, buyers will be implementing projects at their own sites to reduce emissions, such as renewable energy and other low-carbon heat and power generation processes, but they may also want to extend this action to their value chain.
This questionnaire will provide information to buyers on the energy sources used by key suppliers and in the future may be used to identify collaboration opportunities to reduce emissions.
Buyers will therefore use JOSCAR Zero as a platform to collect information on suppliers' greenhouse gas emissions and may want to use this as part of buying decisions when selecting a supplier or identify collaboration opportunities with suppliers to reduce emissions.
Understanding emissions also provides a better understanding of exposure to resource, energy, and climate-related risks.
Why is this of benefit to a supplier?
Suppliers can use greenhouse gas emissions calculating and reporting to monitor their own performance and distinguish themselves from competitors.
By demonstrating that a site has a low or reducing carbon footprint or is using a high proportion of renewable energy, stakeholders will have confidence that organisations are taking appropriate responsibility for their emissions. This also demonstrates a mitigating response to climate risks.
Buyers using JOSCAR Zero are eager to collect information on greenhouse gas emissions and may prefer to work with suppliers that can provide the information and show an understanding of greenhouse gas emissions sources and reporting.
Completing your JOSCAR Zero questionnaire
Scope 1
Natural Gas
What is it?
Natural gas is a fossil fuel that is primarily composed of methane (CH4) and small amounts of other gases such as ethane, propane, butane, and nitrogen. It is formed deep beneath the earth's surface over millions of years from the remains of plants and animals.
Where will it be used onsite?
It is most commonly used onsite in boilers for space heating and generating hot water and steam but may also be used for cooking, for example in a canteen. Boilers are most commonly located in site plant rooms.
Where can you find the information for this question?
The information to answer this question, in order of suitability, is as follows (1 being the most suitable):
- Direct meter readings taken on site, or taken from supplier bill
- Supplier bill based on estimated consumption - it will be stated on the bill if this is the case. Guidance on understanding gas bills and how they are calculated is provided by the UK government and the Centre for Sustainable Energy - https://www.gov.uk/get-help-energy-bills
- Estimated data (refer to the 'Guidance on estimating data' section)
The finance team at the reporting site will be able to provide the bill for the relevant period. If the energy bill is paid by a landlord, it will be necessary to contact them to obtain the direct meter reading or supplier bill.
Units
Kilowatt hour (kWh). This is a measure of total energy from natural gas that has been consumed at the site. If you are reporting in kWh, you will then need to specify if this is being reported in terms of net calorific value (Net CV) or gross calorific value (Gross CV).
Gross calorific value is the maximum amount of energy that can be obtained by burning one kg of a fuel. Gross calorific value is higher than net calorific value as this assumes that water vapour produced from burning the fuel condenses and releases useful energy. It is also known as higher heating value.
Net calorific value is the maximum amount of energy that can be obtained by burning one kg of a fuel. Net calorific value is lower than gross calorific value as the water vapour produced from burning fuel remains as vapour and does not release any useful energy. It is also known as lower heating value.
This can be confirmed by contacting the energy supplier. It is most common for energy billing to be based on Gross CV. If this cannot be found, then Gross CV should be assumed.
Cubic feet or cubic metres. The relevant unit measurement will be shown on the meter.
1hcf = 100ft3
This information can be provided by the plant or utilities engineer, or energy manager at the supplier's site.
The decarbonisation of heating systems is a major challenge in moving towards net zero emissions. It is therefore of interest to understand the proportion of gas use on-site that is used for heating, as this will provide an indication of the requirements for new fuels and processes in the long-term to achieve net zero.
Liquid Petroleum Gas (LPG)
What is it?
Liquid Petroleum Gas (LPG) is a by-product of the petroleum refining process and the extraction of natural gas. LPG is a mixture of propane and butane, with propane being the most common component. It is a colourless, odourless gas in its natural state, but is often compressed and stored in liquid form under moderate pressure to increase its energy density and enable its transportation.
Where will it be used onsite?
LPG is used for heating, cooking, portable heaters, welding, and powering forklifts and other small vehicles. It is most commonly supplied to the site in cylinders or delivered by freight and stored in a tank onsite.
Where can you find the information for this question?
The information to answer this question, in order of suitability, is as follows (1 being the most suitable):
- Records of storage tank level gauge readings or cylinder consumption.
- Supplier delivery invoice to estimate consumption
- Estimated data (refer to the 'Guidance on estimating data' section)
Tank level gauge - The most suitable method will be records of tank level gauge or cylinder consumption. If LPG is stored onsite in a tank, the level gauge can be used to track consumption. This needs to consider any new supply of gas that has been added to the tank in between measuring periods.
Cylinders - Alternatively, LPG consumption can be found from the number of cylinders consumed onsite. The cylinder size will be displayed on the cylinder, and the number of cylinders consumed during the reporting period should be recorded.
The site's plant or utilities engineer will be able to confirm where on site LPG is stored in a tank or cylinders and the record of consumption.
Supplier delivery invoice - the LPG supplier invoice will state the volume or mass of LPG delivered to the site.
The finance team at the reporting site will be able to provide the supplier invoice for the relevant period.
If LPG is only delivered once a year by the fuel supplier, the delivery amount can be taken as the consumption for that reporting year.
Units
LPG can be reported in litres or tonnes.
Diesel
What is it?
Diesel is a type of fuel that is commonly used in diesel engines, which are found in many types of vehicles and heavy equipment, as well as in industrial and commercial settings. It is a liquid fuel that is derived from crude oil through a refining process.
Vehicles
Where will it be used onsite?
Vehicles associated with the site refers to vehicles that are stored at the site when not in use. This should not include vehicles from any other site's in the organisation that are temporarily visiting.
Diesel will be used for vehicles associated with the site in road vehicles that the company owns or operates, and for off-road vehicles such as maintenance vehicles, tractors, excavators.
Where can you find the information for this question?
The information to answer this question, in order of suitability, is as follows (1 being the most suitable):
- Records of litres of diesel used to refuel vehicles.
- Records and estimates of vehicle distance travelled.
- Spend on diesel fuel.
- Estimated data (refer to the 'Guidance on estimating data' section)
Refuel records - this can be obtained from fuel cards and expense claims. The diesel consumption in litres should be stated on the fuel card record, or receipt supporting an expense claim.
Fuel card records can be provided by the finance team or the site's vehicle fleet manager.
Onsite fuelling station - if there is a fuelling station onsite, records of diesel dispensed to vehicles in litres should be obtained. This will provide the information related to diesel consumption for any off-road vehicles onsite. The supplier invoice for delivery to the station can alternatively be used to obtain diesel consumption through the litres of diesel delivered to the site.
The site's utilities engineer, or finance team will be able to provide this information.
If diesel is only delivered once a year by the fuel supplier, the delivery amount can be taken as the consumption for that reporting year.
Distance travelled - if the volume is not available, diesel consumption can be estimated from records of distance travelled. Online maps can be used to estimate the distance for a route travelled by the vehicle that consumes diesel. This should then be multiplied by the number of trips made for this route to calculate distance.
The fleet manager should be able to provide this information.
Spend - if neither of the previous methods are available, the spend on diesel obtained from expense claims and supplier invoices can be used. This should include VAT to align with the conversion factor and avoid errors in under reporting.
This information can be provided by the finance team, or if applicable the site's vehicle fleet manager.
Units
Diesel can be reported in the following units:
- Litres.
- Kilometres, to estimate consumption based on distance travelled.
- Miles, to estimate consumption based on distance travelled.
- £GBP, to estimate consumption based on spend on diesel fuel. Any foreign currency should be converted to £GBP using the exchange rate at the time of transaction.
Stationary Equipment
Where will it be used onsite?
This question refers to diesel that is used onsite for any purpose other than vehicle fuel, diesel is commonly used onsite as a heating fuel and in back-up generators in the event of a power cut. Please do not include combined heat and power (CHP) fuel.
Where can you find the information for this question?
The information to answer this question, in order of suitability, is as follows (1 being the most suitable):
- Records of storage tank level gauge readings.
- Supplier delivery invoice to estimate consumption.
- Estimated data (refer to the 'Guidance on estimating data' section).
Tank level gauge - if diesel is stored onsite in a tank, the level gauge can be used to track consumption. This needs to consider any new supply of fuel that has been added to the tank in between measuring periods. The site's plant or utilities engineer will be able to confirm where on site diesel is stored and the record of consumption.
Supplier delivery invoice - the supplier invoice will state the amount of diesel delivered to the site and/ or the associated cost.
The finance team at the reporting site will be able to provide the supplier invoice for the relevant period.
If diesel is only delivered once a year by the fuel supplier, the delivery amount can be taken as the consumption for that reporting year.
Units
Diesel can be reported in litres or £GBP equivalent.
Petrol
What is it?
Petrol, also known as gasoline, is a type of liquid fuel that is used to power internal combustion engines in vehicles, such as cars, motorcycles, and small planes. It is derived from crude oil through a refining process.
Vehicles
Where will it be used onsite?
Vehicles associated with the site refers to vehicles that are stored at the site when not in use. This should not include vehicles from any other site's in the site's parent organisation that are temporarily visiting. Petrol will be used for vehicles associated with the site in road vehicles that the company owns or operates.
Where can you find the information for this question?
The information to answer this question, in order of suitability, is as follows (1 being the most suitable):
- Records of litres of petrol used to refuel vehicles.
- Records and estimates of vehicle distance travelled.
- Spend on petrol fuel.
- Estimated data (refer to the 'Guidance on estimating data' section)
Refuel records - this can be obtained from fuel cards and expense claims. The petrol consumption in litres should be stated on the fuel card record, or receipt supporting an expense claim.
Fuel card records can be provided by the finance team or the site's vehicle fleet manager.
Onsite fuelling station - if there is a fuelling station onsite, records of petrol dispensed to vehicles in litres should be obtained. This will provide the information related to petrol consumption for any off-road vehicles onsite. The supplier invoice for delivery to the station can alternatively be used to obtain petrol consumption through the litres of diesel delivered to the site.
The site's utilities engineer, or finance team will be able to provide this information.
If petrol is only delivered once a year by the fuel supplier, the delivery amount can be taken as the consumption for that reporting year.
Distance travelled - if the volume is not available, petrol consumption can be estimated from records of distance travelled. Online maps can be used to estimate the distance for a route travelled by the vehicle that consumes petrol. This should then be multiplied by the number of trips made for this route to calculate distance.
The fleet manager should be able to provide this information.
Spend - if neither of the previous methods are available, the spend on petrol obtained from expense claims and supplier invoices can be used. This should include VAT to align with the conversion factor and avoid errors in under reporting.
This information can be provided by the finance team, or if applicable the site's vehicle fleet manager.
Units
Petrol can be reported in the following units:
- Litres.
- Kilometres, to estimate consumption based on distance travelled.
- Miles, to estimate consumption based on distance travelled.
- £GBP, to estimate consumption based on spend on petrol fuel. Any foreign currency should be converted to £GBP using the exchange rate at the time of transaction.
Stationary Equipment
Where will it be used onsite?
This question refers to petrol that is used onsite for any purpose other than vehicle fuel, petrol is commonly used onsite as a fuel for back-up generators in the event of a power cut. Please do not include combined heat and power (CHP) fuel.
Where can you find the information for this question?
The information to answer this question, in order of suitability, is as follows (1 being the most suitable):
- Records of storage tank level gauge readings.
- Supplier delivery invoice to estimate consumption.
- Estimated data (refer to the 'Guidance on estimating data' section).
Tank level gauge - if petrol is stored onsite in a tank, the level gauge can be used to track consumption. This needs to consider any new supply of fuel that has been added to the tank in between measuring periods.
The site's plant or utilities engineer will be able to confirm where on site petrol is stored and the record of consumption.
Supplier delivery invoice - the supplier invoice will state the amount of petrol delivered to the site and/ or the associated cost.
The finance team at the reporting site will be able to provide the supplier invoice for the relevant period. If petrol is only delivered once a year by the fuel supplier, the delivery amount can be taken as the consumption for that reporting year.
Units
Petrol can be reported in litres or £GBP equivalent.
Heating oil/kerosene
What is it?
Heating oil, also known as kerosene, is a type of fuel that is used to heat homes, buildings, and other indoor spaces. It is a liquid fuel that is typically derived from crude oil, and is similar in composition to diesel fuel.
Where will it be used onsite?
Kerosene is most commonly used for heating in older sites or sites that do not have a natural gas grid connection. It is commonly stored in a tank onsite and consumed in the heating system.
Where can you find the information for this question?
The information to answer this question, in order of suitability, is as follows (1 being the most suitable):
- Records of storage tank level gauge readings.
- Supplier delivery invoice to estimate consumption.
- Estimated data (refer to the 'Guidance on estimating data' section).
Tank level gauge - if kerosene is stored onsite in a tank, the level gauge can be used to track consumption. This needs to consider any new supply of fuel that has been added to the tank in between measuring periods.
The site's plant or utilities engineer will be able to confirm where on site kerosene is stored and the record of consumption.
Supplier delivery invoice - the kerosene supplier invoice will state the mass or volume of kerosene delivered to the site.
The finance team at the reporting site will be able to provide the supplier invoice for the relevant period.
If kerosene is only delivered once a year by the fuel supplier, the delivery amount can be taken as the consumption for that reporting year.
Units
Kerosene can be reported in litres or tonnes.
Fuel oil
What is it?
Fuel oil is a type of liquid fuel that is derived from crude oil and used primarily in industrial and commercial settings, such as for powering large ships or for heating and generating electricity in power plants. It is also commonly used as a backup fuel for home heating systems in areas where natural gas is not available.
Where will it be used onsite?
Fuel oil is commonly used as a boiler fuel in steam boilers and in generators that act as a power supply back-up in case of a power cut.
Where can you find the information for this question?
The information to answer this question, in order of suitability, is as follows (1 being the most suitable):
- Records of storage tank level gauge readings.
- Supplier delivery invoice to estimate consumption.
- Estimated data (refer to the 'Guidance on estimating data' section).
Tank level gauge - if fuel oil is stored onsite in a tank, the level gauge can be used to track consumption. This needs to consider any new supply of fuel that has been added to the tank in between measuring periods.
The site's plant or utilities engineer will be able to confirm where on site fuel oil is stored and the record of consumption.
Supplier delivery invoice - the fuel oil supplier invoice will state the mass or volume of fuel oil delivered to the site.
The finance team at the reporting site will be able to provide the supplier invoice for the relevant period.
If fuel oil is only delivered once a year by the fuel supplier, the delivery amount can be taken as the consumption for that reporting year.
Units
Fuel oil can be reported in litres or tonnes
Gas oil
What is it?
Gas oil is a type of fuel oil that is derived from crude oil through a refining process, and is commonly used in industrial and commercial settings for heating, powering engines, and generating electricity.
Where will it be used onsite?
Gas oil, also known as red diesel, is commonly used as a fuel for off-road vehicles such as tractors and trucks. It can also be used for heating and in back-up generators.
Where can you find the information for this question?
The information to answer this question, in order of suitability, is as follows (1 being the most suitable):
- Records of storage tank level gauge readings.
- Supplier delivery invoice to estimate consumption.
- Estimated data (refer to the 'Guidance on estimating data' section).
Tank level gauge- if gas oil is stored onsite in a tank, the level gauge can be used to track consumption. This needs to consider any new supply of fuel that has been added to the tank in between measuring periods.
The site's plant or utilities engineer will be able to confirm where on site gas oil is stored and the record of consumption.
Supplier delivery invoice - the gas oil supplier invoice will state the mass or volume of gas oil delivered to the site.
The finance team at the reporting site will be able to provide the supplier invoice for the relevant period.
If gas oil is only delivered once a year by the fuel supplier, the delivery amount can be taken as the consumption for that reporting year.
Units
Gas oil can be reported in litres or tonnes.
Combined heat and power (CHP) system
What is it?
A CHP system, or Combined Heat and Power system, is a type of energy generation system that simultaneously produces electricity and useful heat from a single fuel source.
In a CHP system, fuel is burned to generate electricity using a generator, and the waste heat from the combustion process is captured and used to generate hot water or steam for heating or other industrial processes. The heat can also be used for cooling through absorption chillers or other cooling technologies.
CHP systems are used in a wide range of applications, including commercial and industrial facilities, hospitals, universities, and district heating systems. They can be powered by a variety of fuels.
Where will it be used onsite?
A CHP unit will be located in the site's plant room.
Where can you find the information for this question?
The site should consult with plant or utilities engineers to understand if there is a CHP system onsite and the type of fuel(s) consumed in the CHP.
The amount of fuel consumed in the CHP can be obtained from meter records - the CHP will have a fuel supply meter providing this information.
The plant or utilities engineer can provide the fuel supply meter readings.
For further guidance, please refer to the 'Natural Gas', 'Heating oil/kerosene' and 'Diesel' sections.
Units
The fuel consumption should be entered for all relevant CHP fuels.
If the CHP consumes more than one fuel, data should be entered for all those that apply.
Natural gas can be reported in terms of energy, in kWh, or in terms of volume in cubic metres, m3, and hundreds cubic feet, hcf.
Biomass (wood pellets) should be reported in tonnes.
Heating oil/kerosene can be reported in litres or tonnes.
Diesel can be reported in litres or tonnes.
Biomass (non CHP)
What is it?
Biomass refers to organic matter that can be used as a source of energy.
Where will it be used onsite?
Biomass is commonly used onsite in steam boilers and for space heating. This question excludes any biomass that is consumed in a CHP.
Where can you find the information for this question?
The supplier invoice can be used to obtain biomass consumption, as it will state the amount of biomass delivered to the site.
The site's finance team will be able to provide the invoice for the relevant reporting period.
The biomass should be reported by physical state of the wood consumed. Wood logs, the largest form of wood fuel, wood chips, which are logs cut into smaller cubes, or wood pellets, the smallest form, which have been compressed.
Units
The consumption information should be entered for all relevant biomass types in tonnes.
If more than one biomass type is used, data should be entered for all those that apply.
Refrigerants
What is it?
Refrigerants are substances that transfer heat from one location to another. They are typically liquids or gases that have low boiling points and are able to absorb heat when they evaporate and release heat when they condense.
Where will it be used onsite?
These fluids are used in cooling systems such as air-conditioning systems and cold storage.
Where can you find the information for this question?
The information will be provided in the equipment that uses refrigerants' maintenance record. As part of the required periodic maintenance for refrigeration systems, a contractor will top-up the refrigerant fluid that has leaked from the system. This maintenance record will state the refrigerant used in the system and the amount that has leaked can be reported as the amount added to the system by the contractor.
The site's utilities engineer, or maintenance engineer will be able to help find this information and previous records of maintenance.
Units
The refrigerants onsite should be selected from their categories, and the consumption information should be entered for all relevant refrigerants used in tonnes, a measure of consumption by mass.
If more than one refrigerant is used, data should be entered for all those that apply.
Scope 2
Grid electricity
What is it?
Grid electricity refers to the electricity that is generated from power plants and distributed through a network of transmission lines and distribution substations, commonly known as the power grid or electric grid.
Where will it be used onsite?
It is expected that all sites will have an electricity supply. In many cases this will be supplied by the local grid network.
Grid electricity will be supplied to the site by an energy supplier. Electricity will then be used throughout the site for powering equipment and processes such as lighting, computer systems, etc.
Where can you find the information for this question?
The information regarding consumption amount to answer this question, in order of suitability, is as follows (1 being the most suitable):
- Direct meter readings taken on site, or taken from supplier bill,
- Supplier bill based on estimated consumption.
- Estimated data (refer to the 'Guidance on estimating data' section).
The consumption of electricity will be stated on the electricity invoice or bill and will be in kWh. This has been determined from the electricity meter(s) installed onsite.
Meter readings - the site should speak to the plant engineer or utilities engineer to find out where the meter is located, this should be the meter for all incoming electricity to the site. The meter will have to be read at regular intervals so that the latest reading can be subtracted from the previous reading to obtain the cumulative consumption.
The electricity bill will state if the bill is based on estimated consumption, the site can obtain the electricity bill from the finance team. If this is the case, the site should first try to obtain direct meter readings as the most suitable information to answer the question.
In order to determine the supplier of electricity, this will be stated on the electricity invoice or bill. If the site has used more than one supplier in the reporting period, the site will need to provide information on all suppliers.
Units
The default unit for electricity is kWh. This is a measure of total electrical energy that has been consumed at the site.
Supplier specific emissions factors
Where can you find the information for this question?
An emission factor is used to calculate the amount of greenhouse gases emitted from an activity.
As electricity is generated from a number of different fuels and sources, typically an average emission factor is used when purchasing electricity from the grid. However, accuracy in calculating electricity associated emissions can be improved if a supplier specific factor is used. This factor will have been determined based on the fuels used for electricity by the supplier.
The supplier specific emission factor is a ratio of the equivalent mass of CO2 in kg and electrical energy in kWh, the units being kgCO2e/ kWh. If the supplier emission factor is provided in CO2 g/ kWh, this can be converted to kgCO2e/ kWh by dividing by 1000.
Information on amount of electricity purchased through supplier specific emissions contracts can be obtained in the same way as that for grid electricity (please see 'Grid Electricity' section.)
The supplier specific emissions factor can be found on the electricity supplier's website or by contacting the electricity supplier.
If the site has had more than one electricity supplier in the reporting period, the site will need to contact all electricity suppliers. The supplier specific emission factor will be valid for a finite period of time; therefore, the specific emission factor must be applicable for the site's reporting period.
Zero emissions contracts
What is it?
It is possible to negotiate a contract with the electricity supplier for the electricity supplied to be zero emissions.
Many companies cannot produce renewable energy onsite but wish to purchase renewable electricity to reduce their carbon footprint. This is supported by a certificate of origin. The most common form in the UK is a Renewable Energy Guarantee of Origin (REGO) .
Although not categorised as a renewable fuel, zero emissions contracts are also available through the supply of 100% nuclear generated electricity. If the site's electricity contract is for the supply of 100% nuclear energy, this can be submitted in response to this question, with the supplier certificate or electricity invoice stating the supply is nuclear generated electricity as supporting evidence.
Where can you find the information for this question?
Information on amount of electricity purchased through zero emissions contracts can be obtained in the same way as that for grid electricity (see 'Grid Electricity section).
If the site is purchasing zero emissions electricity through a nuclear contract, the amount of electricity invoiced for the reporting period should be used to answer the question. This will be stated on the invoice. The site's finance team will be able to provide the electricity invoice.
REGO certificates
Companies that consume electricity can purchase REGOs from third parties for the amount of electricity they have consumed that they wish to be zero emission and claim that electricity amount as zero emission. The amount of electricity that the REGO guarantees as zero emission will be stated on the certificate. Renewable electricity that is not supported by certification cannot be claimed as zero emissions. The site should upload the REGO certificate purchased in the upload box.
The site's finance team will be able to help obtain the REGO certificate or this can be obtained from the certificate supplier.
Renewable energy
Onsite generated
Electricity can be generated onsite from renewable sources as a zero-emission source of energy and consumed at the site to reduce operating costs and emissions. This information will be useful to buyers to understand the type of renewable energy onsite and the amount of electricity consumed.
The amount of renewable energy consumed on site can be determined from the installed meter or desktop reporting system provided with the installation. Renewable installations will supply a consumption meter linked to the site's existing electricity system and this should be read at regular intervals to collect the required information.
The site's plant or utilities engineer will be able to provide this information.
The default unit for electricity is kWh. This is a measure of total renewable electricity that has been consumed by the site after generating onsite.
Private agreement
Renewable electricity can be reported as zero emission electricity. Rather than generating onsite or purchasing REGOs, a company can negotiate a private supply of renewable energy directly from a generator, this question seeks to understand if the site has such an agreement in place.
A private agreement supply can be cheaper than buying from the electricity grid and is favoured by some companies who want a dedicated source of renewable electricity. An example would be the owner of unused land adjacent to the site installing solar panels and selling the generated electricity direct to the site.
The site's finance team can confirm if the site has a private agreement supply in place for electricity.
To answer this question the amount of electricity supplied is required. Information on amount of electricity purchased through private agreement supply can be obtained in the same way as that for grid electricity (see 'Grid Electricity' section).
The default unit for electricity is kWh. This is a measure of total electrical energy that has been supplied by private agreement to the site.
Heat and steam
Where can you find the information for this question?
Some companies choose to purchase heat and/ or steam from a third party, for reasons such as not having the equipment on site, spatial restrictions etc. Heat will commonly be in the form of hot water in the temperature range 40°C to 95°C.
The information regarding amount of purchased heat and/ or steam to answer this question, in order of suitability, is as follows (1 being the most suitable):
- Direct meter readings taken on site, or taken from supplier bill.
- Supplier bill based on estimated consumption.
- Estimated data (refer to the 'Guidance on estimating data' section).
The amount of heat and/ or steam that has been purchased should be obtained from meter readings at the point of supply.
The site’s plant engineer or utilities engineer will be able to provide this information.
The site’s finance team will be able to provide the invoice with the required information for the reporting period. The supplier invoice will state if the bill is based on estimated consumption, if this is the case, the site should first try to obtain direct meter readings as the most suitable information to answer the question.
Units
The default unit for heat and/ or steam is kWh. This is a measure of total heat and/ or steam energy that has been supplied to the site.
Scope 3
Mains water
Where can you find the information for this questions?
Mains water will be supplied by the local water company and used onsite for cleaning, sanitary, and some production activities such as steam generation, and cooling of manufacturing equipment.
The information to answer this question, in order of suitability, is as follows (1 being the most suitable):
- Direct meter readings taken on site, or taken from supplier bill
- Supplier bill based on estimated consumption
- Estimated data (refer to the 'Guidance on estimating data' section)
The site should consult with plant or utility engineers to obtain direct meter readings.
The water bill will state if the bill is based on estimated consumption, the site can obtain the water bill from the finance team. If this is the case, the site should first try to obtain direct meter readings as the most suitable information to answer the question.
Units
The default unit for water consumption is cubic metres, m3. This is a measure of total water that has been supplied to the site.
Waste
Types of waste
The waste data will be reported by type of waste. It is good practice to separate waste on site by material before disposal.
The following categories are provided:
- Construction waste: associated with building and renovation activities onsite and includes materials such as concrete, bricks, insulation etc.
- Refuse: common types of waste such as household residual waste, organic: food and drink waste etc.
- Electrical: this is legally referred to as waste electrical and electronic equipment (WEEE ) and refers to any electronic waste disposed of by the site that must be disposed of separately such as fridges and freezers, batteries etc.
- Metal: this refers to any waste that is metal material such as scrap metal, steel cans, etc.
- Plastic: this refers to any waste that is plastic material such as PET, HDPE etc.
- Paper: this refers to any waste that is paper material, including cardboard such as paper, cardboard, or mixed.
- Other: this category includes books, glass, and clothing
Where can you find the inforation for this question?
The information to answer this question, in order of suitability, is as follows (1 being the most suitable):
- Waste weight measurements taken on site, or taken from supplier bill
- Supplier bill based on estimated generated waste
- Estimated data (refer to the 'Guidance on estimating data' section)
The waste data will be available from the site’s waste disposal contractor. Many contractors will provide a report for clients detailing the types of waste and the disposal methods for the waste.
Alternatively, this information should be in the invoice sent for disposal of waste on a weekly, biweekly, or monthly basis.
The site’s finance team can provide a copy of the invoice.
Units
The types of waste onsite should be selected from their categories, and the consumption information should be entered for all waste disposed of in tonnes.
If more than one type of waste is disposed of, data should be entered for all those that apply.
Scope 3 emissions
Types of scope 3 emissions
Some organisations will be further along in their reporting journey and may have calculated scope 3 emissions themselves for a wider range of categories. This aspect of the questionnaire is designed to capture the information available in those circumstances.
Scope 3 emissions cover all value chain activities. In order to fully understand an organisation’s scope 3 emissions and identify activities with relatively high emissions, they are reported in 15 different categories:
- Purchased goods and services
- Capital goods
- Fuel and energy related activities
- Upstream transportation and distribution
- Waste generated in operations
- Global business travel
- Employee commuting
- Upstream leased assets
- Downstream transportation and distribution
- Processing of sold products
- Use of sold products
- End-of-life treatment of sold products
- Downstream leased assets
- Franchises
- Investments
Where can you find the information for this question?
This information will be from calculations already performed by the site. Guidance for how to calculate each category is available from the GHG Protocol - https://ghgprotocol.org/scope-3-calculation-guidance-2.
The site’s environmental health and safety (EHS) team will be able to provide this information.
Please ensure the scope 3 carbon emissions data is for this site and not at entity level. Scope 3 carbon emissions should be entered in your JOSCAR questionnaire.
Guidance on estimating data
The intention of this questionnaire is to collect accurate and up-to-date information from suppliers. If the data is of high quality, then it will produce better outcomes which can inform the decision-making process. In the event that information cannot be collected by the site, the following methods are available for estimating data:
- Pro-rata consumption if information for the full year is not available
- Historic comparison
- Spend-based method
- Similar site as proxy
Pro-rata consumption method
Pro-rata consumption involves estimating the data for the full year based on an incomplete data set, for example if data for two months of the year is missing.
The site should use the following method to calculate pro-rata consumption:
(1). Review the information you have available for consumption (example 1,000,000 kWh).
(2). Count the number of days of the year the information is missing for (example: 61 days).
(3). Count the number of days of the year information in (2) is available for (example: 304 days).
(4). Divide the number of days in (2) by the number of days in (3) and multiply by the consumption in (1) to estimate the consumption for the missing days (example 1,000,000 x 61/304 = 200,657.89 kWh).
(5). Add the estimated consumption in (4) to the available consumption in (1) to get the estimated consumption for the full year (example 1,000,000 + 200,657.89 = 1,200,657.89 kWh).
Historic comparison method
Historic comparison involves using the consumption from the same month for the previous year in the event of missing information.
The site should use the following method for historic comparison:
(1). Identify the month for which information is missing (example February 2022).
(2). Obtain the information for the month in (1) from the data for the previous year (example February 2021 = 1,500 kWh).
(3). Add the information from (2) to the information for the current year to estimate for the full year.
Spend-based calculation method
This can be used when information is only available in terms of monetary spend on energy.
The site should use the following method for the spend-based calculation:
(1). Contact the finance team to obtain record of spend associated with the activity during the reporting period (example £0.5 million GBP on gas oil in 2022).
(2). Download the UK government energy price reports for the four quarters of the reporting period (example March 2022, June 2022, September 2022, and December 2022). The price for the fuel being reported should then be obtained in £GBP/ kWh. If the site is based outside the UK, you will need to download your country’s equivalent report.
(3). If the spending in (1) can be broken down by quarter of the year, multiply each quarterly spend amount by the reported price for that fuel at the time.
(4). If the spending in (1) cannot be broken down by quarter of the year, the four prices should be added together and divided by four to estimate an average price for the entire year.
(5). The result of the calculation in (3) or (4) should be input to the questionnaire.
Similar site as proxy
If the entity has more than one site and has information for another site but not the site completing the questionnaire, the site can use the information from the similar site to estimate for the reporting site through the following method:
(1). Obtain the floor area of the site that is missing information (example Site A = 5,000m2).
(2). Obtain the floor area of the site that has the reporting information but is not completing the questionnaire (example Site B = 7,500m2). The floor area for both sites should be in the same units.
(3). Obtain the reporting information (e.g. natural gas consumption) for the site in (2) (example Site B = 9,000 kWh).
(4). Divide the floor area of the site missing information by the floor area for the site that has the information and then multiply by the information in (3) (example 5,000/7,500 x 9,000 = 6,000 kWh).
(5). The result of the calculation in (4) should be input to the questionnaire.
If floor area for both sites is not available, the site can also use number of employees or production volume. The same units must be used for both sites.
How to upload documents
Some questions will require you to also upload a document.
It is important to upload documents to help demonstrate your compliance to the buyers in the community.
When uploading a document, first, answer the question (or questions).
Use the 'UPLOAD' button to upload the document from your computer.
Please note: All documents must be uploaded in PDF format only and be no larger than 25Mb.
Uploaded documents can be removed simply by clicking the ‘bin’ icon next to the document.
Buyer specific questions
The questionnaire includes buyer specific questions asking what percentage of output from that site is attributable to each of the buying organisations that have nominated the site to complete.
How to submit the questionnaire
Once you have answered all mandatory questions, your questionnaire will be ready to be submitted.
To submit your questionnaire, click the SUBMIT button.
Note: If the button is not active (greyed-out), please check you have answered all mandatory questions..
Before submitting your questionnaire you'll be asked to complete the declaration.
After submitting your questionnaire, you will notice that all question fields are now locked for edit. Your questionnaire will remain in this state until you unlock your questionnaire to complete an update or renewal.
How to get help and support
How to get additional help and support
The JOSCAR Supplier Support Team are on hand to help with any questions you may have. You can contact them via joscar@hellios.com or +44 (0)1865 959110. Support hours are Monday to Friday, 8.30am to 5.30pm UK time excluding UK public holidays.
Understanding your JOSCAR Zero Dashboard
Filters
Year
This is the year entered into the JOSCAR Zero Questionnaire (please note emission factors are at least mid-year. E.g. if date entered is 07/2022 - 12/2022, year shown would be 2023)
Selected Site(s) Emissions
This filter allows you to select which site you would like to view the data for. The default will show all sites that are published on JOSCAR Zero.
Emissions
How has the dashboard been calculated
The most widespread GHG is carbon dioxide (CO2), and this is used as a standard measure for GHG emissions by converting all other GHGs to the equivalent mass of CO2. This unit is referred to as a tonne of carbon dioxide equivalent, tCO2e.
The GHG emissions arising from human activities can be calculated by using conversion factors, known as emission factors. These are expressed in terms of kgCO2e per unit of activity. The denominator for the emission factor will depend on the activity type.
JOSCAR Zero is aligned to the GHG Protocol and uses emissions factors published by the UK Government and the IEA.
Total Emissions
This is the sum of all emissions for scope 1, 2, and 3. This is calculated from the data provided in the JOSCAR Zero Questionnaire.
Average Emissions Intensity
This is the average emissions per head per site i.e. average (total emissions / total employees). An emission intensity metric is commonly used by companies for purposes such as a key performance indicator (KPI) and to benchmark against industry peers.
Working towards Net Zero
This is based on your response to Q2.7.13 in the JOSCAR Questionnaire. For help in updating your questionnaire, please click here.
Renewable energy
This is the percentage of the total energy usage that is supplied through renewable sources (either onsite generated or purchased).
Supplier Emissions (tCO2e)
This chart tracks your total emissions each year and also shows them divided by scope.
Emissions (tCO2e)
This shows the ranking of your sites or countries by emissions (the country is based on each site location). The default sort is largest to smallest.
Emission Sources (tCO2e)
This is a list of your emission sources grouped by scope. The scope percentage equals the proportion of each source compared to the scope. The total percentage shows the comparison of the sources against all scopes.
Understanding your JOSCAR Zero Carbon Action Plan(s)
What is a Carbon Action Plan?
A Carbon Action Plan is a strategic document that outlines specific actions and initiatives an organisation will undertake to reduce its carbon emissions and mitigate its impact on climate change.
The plan typically includes target completion timelines, and detailed steps for achieving carbon reduction goals.
It is an essential component of an organisation's sustainability strategy and demonstrates its commitment to environmental responsibility. A Carbon action Plan can support the creation of a Carbon Reduction Plan – link to PPN06/21.
JOSCAR Zero creates one Carbon Action Plan per site, once that site has completed the JOSCAR Zero questionnaire.
What are the benefits of Carbon Action Plans?
Regulatory Compliance: Ensures the organisation meets or exceeds environmental regulations and standards.
Cost Savings: Identifies opportunities for energy and resource efficiency, leading to cost reductions.
Reputation Enhancement: Demonstrates a commitment to sustainability, which can enhance company reputation with customers and employees.
Risk Management: Mitigates risks associated with climate change, such as regulatory penalties, supply chain disruptions, and physical impacts.
Innovation and Competitiveness: Encourages innovation and positions the organisation as a leader in sustainability, potentially opening up new markets and opportunities.
Where can I find my JOSCAR Zero Carbon Action Plan(s)?
Your tailored JOSCAR Zero Carbon Action Plan can be found in the JOSCAR portal along with your dashboard and site questionnaires.
For help with logging on to the JOSCAR portal, please visit our website.
When do I need to update my information?
Your JOSCAR Zero Carbon Action Plan(s) can be updated at any time, and we would encourage you to do this regularly to ensure that your organisation’s information is accurate and up to date.
How can we use our JOSCAR Zero Carbon Action Plan(s) to our benefit?
Suppliers that show their commitment and maturity relating to decaronbisation often have a competitive advantage. JOSCAR Zero can be used to support requirements under PPN 06/21.
The content has been provided and tailored by globally renown environmental consultancy firm, Ricardo. Keep up to date on new ways to decarbonize by updating and checking your carbon action plan regularly.
Who will have access to our Carbon Action Plan(s)?
Any data you enter into JOSCAR is owned by you, the supplier. It will only be shared with the buying organisations who are Buyer members of the JOSCAR Zero community and will not be shared with any other third party.
Other suppliers will not have access to the information you provide. It is only available to the buying organisations within the community. Each buying organisation has signed a confidentiality agreement with Hellios.
How have our Carbon Action Plan(s) been tailored to my company?
The content has been provided and tailored by globally renown environmental consultancy firm, Ricardo. These will be updated periodically as new ways to decarbonize come to light.
The system will automatically recommend actions to you based on the information you have provided within your JOSCAR Zero questionnaire, such as the type of site, the amount of natural gas used, if any refrigerants are used etc...
Maintaining your JOSCAR Zero questionnaire
How to renew your JOSCAR Zero questionnaire
The buying organisations require their suppliers to keep their information up-to-date. All suppliers are required to update and re-submit their information annually. Suppliers are notified of the need to renew in advance of their renewal date and this will be scheduled to start once your JOSCAR renewal is complete.
Please note: it is important that you complete renewal by the deadline stated, as this is your anniversary date and cannot be amended or extended.
Where information is available, please include a new reporting period each renewal or update, as this will allow you and your buyers to track your organisation's progress towards net zero over time.
How to update your information
It is important that your information is kept up-to-date at all times. In addition to the annual renewal a process, you will be able to access and update any of your information throughout the year. There are typically a number of key triggers for updating your information:
- A customer has nominated one of your sites to complete the JOSCAR Zero questionnaire, to provide them with visibility of the carbon emissions attributable to them from that site
- Another customer of your company has joined the community and your information needs to be updated to be relevant to the goods or services you supply to them
- New questions have been added to the questionnaire by the buying organisations and they cannot wait for your annual renewal before they are answered
Before making an update, you must first unlock your questionnaire. To do this, log into the system as normal and navigate to your questionnaire. You will notice that the questions are locked and cannot be updated. To unlock them, click the update button highlighted in the image below.
Clicking the button will bring up a confirmation message, click 'YES' to continue to unlock and update your questionnaire.
Any updates you make to your questionnaire will NOT be visible to buyers until your changes have been submitted once more.